
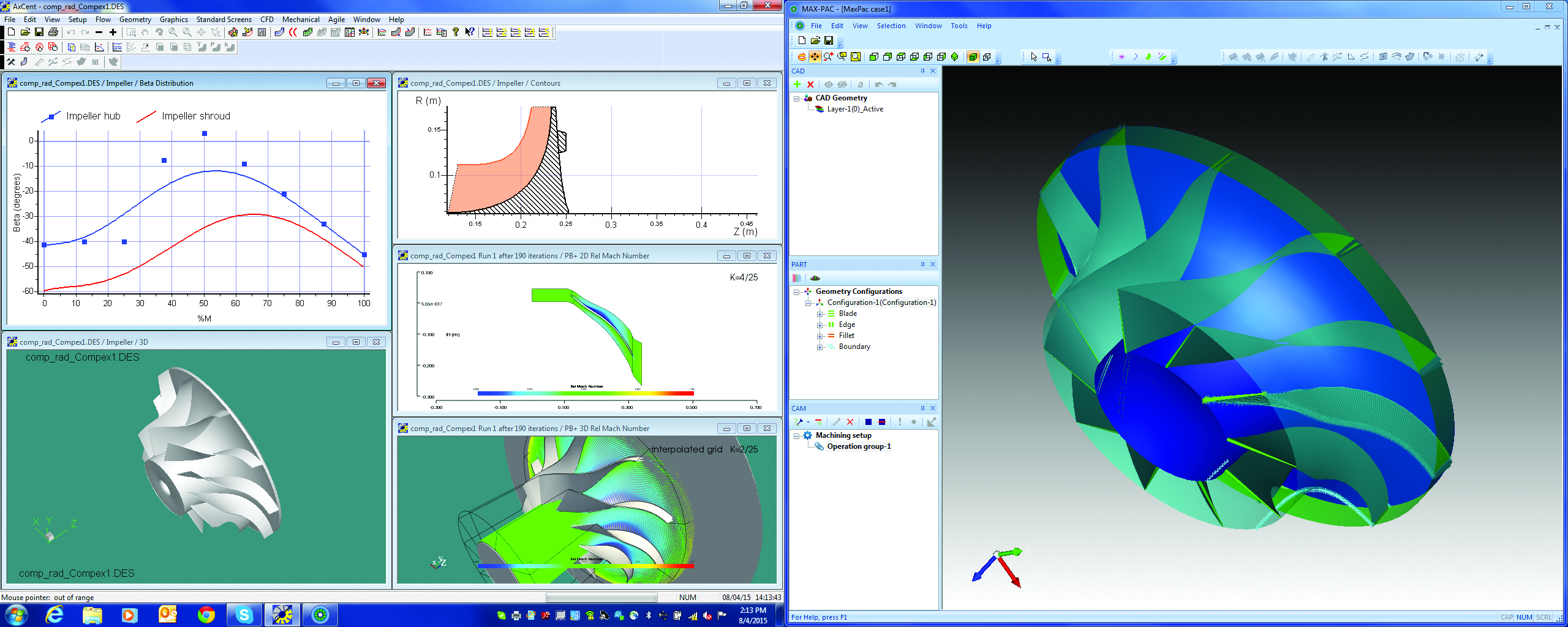
The new stock-pillar-removal feature uses a spiral ramp motion to remove the pillar after the adaptive roughing cycle, thereby eliminating the vibrations and excessive heat to improve the cutting conditions and prolong the tool life.
CAM SOFTWARE BLISK CODE
This pillar can create adverse cutting conditions such as vibrations and localized heat generation. New CAM software algorithms have made programming five-axis mills easier than ever before, including digitally verifying the code for safety once programmed.
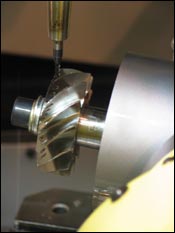
The standard settings for adaptive roughing often leave a pillar at the center of the area being machined. Stock pillar removal for adaptive roughing The toolpath calculation algorithms use “out to in” ordering to remove the material gradually which enables the flatland cycle to machine parts with undercut features. This new option for the flatland cycle enables operators to machine flat undercut areas using slot milling tools.Īdditional toolpath slices are generated on the flat regions of the undercut. Operators can adjust the variable offset at different locations on the blade to fine-tune the toolpath according to measurement results based on the coordinate measuring machine, without changing the complex 3D file. Smooth toolpaths ensure consistent acceleration and, therefore, shorter cycle times. The new blisk module provides parameters and settings for creating very smooth toolpaths for multiblade machining. This is the first major ModuleWorks release of 2022 and contains new and enhanced features across the entire product range, including the new blisk module for multiblade machining, undercut machining with slot mills and stock pillar removal for adaptive roughing. ModuleWorks announces the release of its 2022.04 CAD/CAM software components for digital manufacturing.
